
Pcad 2006 Sch Manual Labor Assembly
The companys PCAD product has been synonymous with PCB design expertise and high quality PCB layout tools.ExpressPCB Plus 2 - 6 layers Silkscreen 2 sides (Top/Bottom) Schematic Link To Layout SnapEDA integration for components Netlist Validation between SCH and.Redistribution and use of this article or any images or files referenced in it, in source and binary forms, with or without modification, are permitted provided that the following conditions are met:2006-2007 Ford Vehicles Workshop Repair Service Manual - 2,000MB DVD 2007 Ford Vehicles Workshop Repair Service Manual - 5GB DVD BEST 2006 - 2011 Ford F250 F350 F450 F550 Super Duty - SERVICE / REPAIR / SHOP MANUAL (MASSIVE 7000 Pages) PRINTABLE - SEARCHABLE - INDEXED - PDF DOWNLOAD FORD F-SUPER DUTY 450 2007 SERVICE MANUALPcad 2006 Library Download. P-CAD2002 PCB design layout tools software P-CAD2002 P-CAD 2006 P-CAD 2006 Service Pack 2 (29.7 MB) P-CAD 2006 Service Pack 2. Manual Labor Assembly Components Procurement Electronic Testing BGA Rework PCB Repair.
1.2.2 Installing PCAD Viewer Since you have access to Schematic suite only, you will need to install the Viewer if you wish to view PCBs created in PCAD. Install Service Pack 1 by going to \\jlabgrp\eecad\pcad\2006\Installation CDs\P-CAD 2006\Service Packs (on the network) and double clicking on the. Redistributions of article must retain the above copyright notice, this list of conditions, link to this page and the following disclaimer.9. CAD translation & Gerber translation software for Netlist conversions.
IntroductionBack in 2008, when I was still a student, for better learning of computer systems operation and embedded devices development, I started this project. In no event shall the author, xDevs.com, or any other 3rd party be liable for any special, direct, indirect, or consequential damages or any damages whatsoever resulting from loss of use, data or profits, whether in an action of contract, negligence or other tortuous action, arising out of or in connection with the use of any information published here. This download includes the entire set of P-CAD 2006 libraries (which are the same set of libraries delivered with P-CAD 2004).All information posted here is hosted just for education purposes and provided AS IS. Pcad 2006 schematic libraries found at jlab.org, vasynet.com.
It’s even better when first design fails. Humans are not designed well to do repetitive monotonic job for long periods of time, while computers and robots are don’t care at all, and can do testing much faster and with good repetitive rate.There is nothing better for learning new stuff than actually trying to build something. Of course, job can be done with instruments like standalone DC loads, multimeters and oscilloscopes to measure add data, and evaluate actual PSU performance on output voltage power rails, but if you need test power supplies every day, or have more than two channels on them, just wiring and adjusting knobs and buttons on test gear become very time ineffective. Of course, there are production systems from leading vendors, such as Chroma ATE or HPAK, but those are out of scope and price reach for small labs.Why someone would need automated machine? Well, if you design power supplies or want to test existing power supply, you must have easy adjustable loading for PSU, so you can stress power supply and ensure its proper operation, both thermally and electrically. Project goal was to build automatic power supply testing unit, or like how they usually called – ATE.
We can use it as a base reference. ATX Power supply design guides give a good idea how PSUs are tested by design and manufacturers. What device will be doing? How it should do it? What way user can control its operation and settings? How to read results and data out of it? Does protection on input signals need to be implemented? If answer is positive, then how well signal should be protected? This are common questions need to be addressed in specification.Let’s define, what power supply tests should this ATE perform. Project and design specificationFirst step of any design, either be it simple circuit with 5 components, or complicated machinery with hundreds of parts, megabytes of firmware and software code in it always should start with a definition of specification. Theory backed up by practical engineering is always a great value for every practical application.
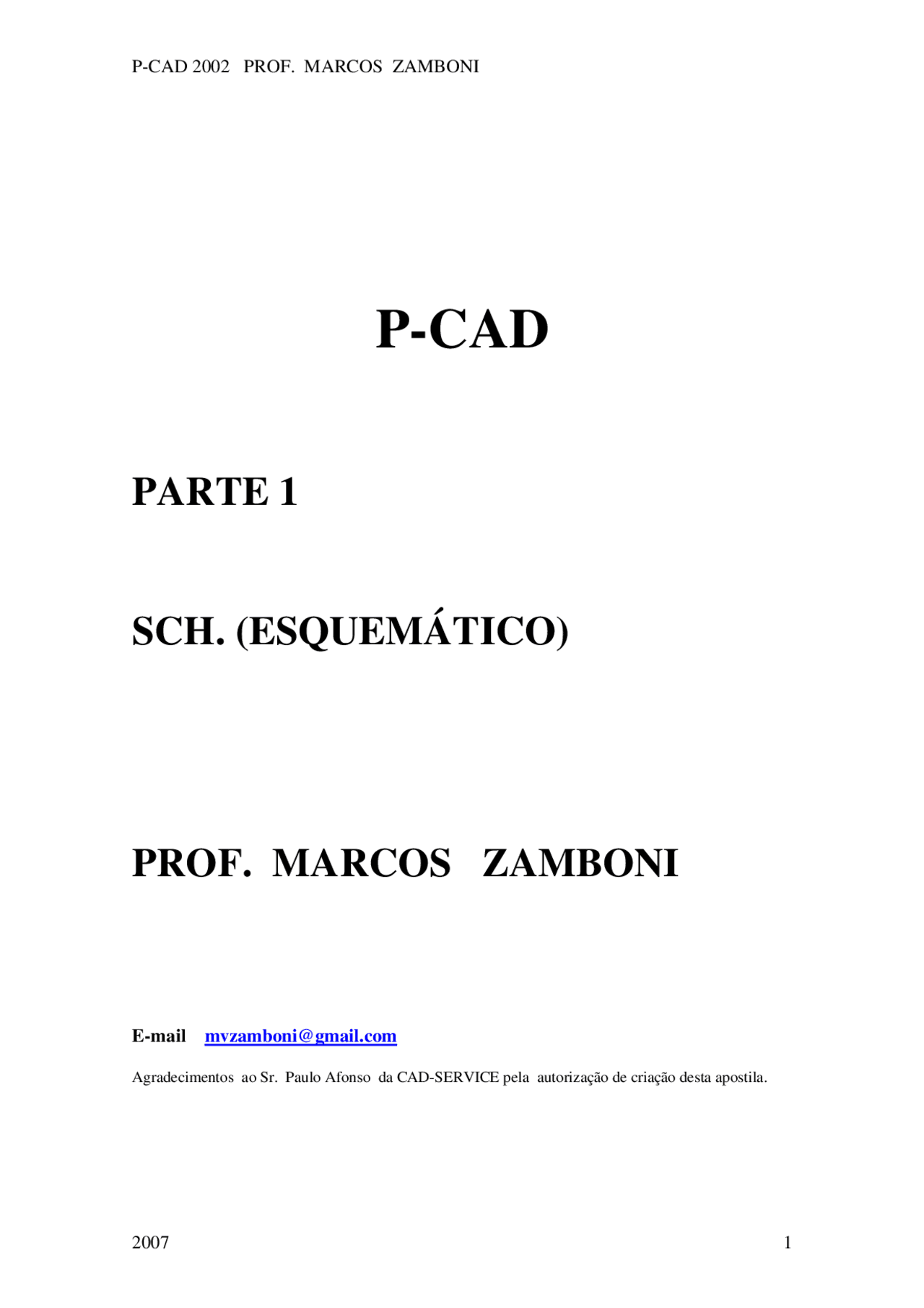
PSU test with close to real application conditions (desktop PC chassis with elevated thermals) Dynamic loading test (variable load over time) Protection testing (overload, overcurrent)
Build worklogDesign workflow, such as schematic design, board layout and overall concept and assembly will be discussed in sections below.As a reference, standard guidelines for ATX power supplies are taken into account, so from PSU DUT point of view our tester would mimic real computer motherboard and peripherals. Unit not intended for tight equipment racks, where cooling usually an issue, so we can try to get away with this spec.Since majority of ATX power supplies are using standard connectors, I choose to have next input interfaces for interconnection with PSU: Input portCPU0 (black, primary, two +12V1&2 channels)CPU1 (white, secondary, two +12V5&6 channels)Table 1: Input connectors and channel definitionThis brings us next requirements for individual voltage channels: Channel numberTarget low cost of implementation, preferred less than $1000 USD. Ambient temperature (operation), 0…+30☌ with power levels 2000WRelaxed ambient temperature spec will allow using cheaper power components for DC load channels, so some cost can be saved. Ambient temperature (operation), 0…+40☌ with power levels 1200W Ambient temperature (operation), 0…+50☌ with power levels 800W

Analog Devices AD8664 quadruple opamp used to allow driving long wires and high-power FETs with large capacitive gates. Few standard 10W ceramic shunts in parallel connection are used.DA13.B and DA13.D are just voltage follower buffers to sense input voltage at DC load and drive ADC inputs for measurements. Shunt resistance is in range 10-20 mΩ to minimize power dissipated in shunt. DA13.C forms amplifier for current signal from low-resistance shunt, located right at FET pins. Based on this, proper heatsink can be calculated and actual MOSFET die temperature can be estimated.Image 1: MOSFET driver schematics, single-channelDA13.A takes input voltage signal from DAC and drive power MOSFETs gate.
So I used pair of paralleled MOSFETs in TO-247 in the final design. For better accuracy or higher frequency dynamic loads location of opamp much closer to MOSFET would be required to minimize inductance and capacitance of all signal nodes.ISOTOP MOSFETs were really reliable at power levels about 350W and nice to use, but they are about $20USD each, so with 12 channels we need cost only on FETs alone would be ~$250 USD already. Since we don’t have very high performance requirements, this approach working okay.
Change of FETs to non-isolated TO-247 also rendered need of mounting heatsinks on Teflon standoffs, as they were under input voltage potential now, and we required separate channels to be isolated. Pair of IRFP90N20D was able to dissipate about 300W power with ambient temperature at +40☌, using Xeon 604 fansink with copper insert plate in base.
